In this article, we delve deeply into the roadmap for achieving exemplary quality in production through the strategic integration of Quality 4.0 into smart manufacturing environments. In an era of relentless pursuit of excellence, output quality has solidified its position as the cornerstone of industrial success and customer satisfaction. As companies navigate the complexities of digital transformation, effectively integrating digital building blocks has become essential for maintaining and elevating quality control standards. The convergence of advanced technology with traditional manufacturing processes drives the evolution toward Industry 4.0, marking a significant shift in how businesses approach production efficiency, compliance with ISO standards, and the overall quality of their products.
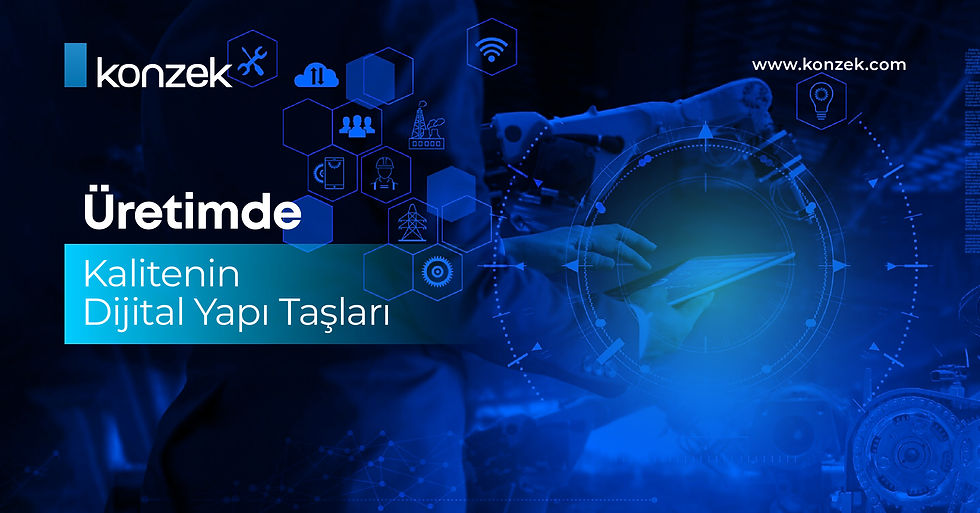
What is Quality Control?
Quality control is the process of ensuring that a product or service meets the defined standards and requirements. Fundamentally, quality control guarantees that the product or service satisfies customer expectations and is free from defects, deficiencies, or deviations. This process aims to secure quality through various inspections, tests, and examinations conducted during and after production.
Quality control aims to improve the product and the production processes, enhance customer satisfaction, and reduce costs. This approach is supported by statistical methods, process controls, and continuous improvement (Kaizen) in modern manufacturing systems, aiming to increase efficiency and minimize errors. After this basic definition, let's explore quality control's historical evolution and development.
Evolution and History of Quality Control
The historical evolution of quality control is closely linked to the development of production processes, spanning from the earliest periods of human history to the present day. In the early days, quality control was a simple process in which master artisans inspected their products to ensure quality. In the Middle Ages, guild systems developed rules to ensure that products met specific standards and established a system for quality control. Guilds required masters to use their marks to guarantee product quality, a practice considered one of the first steps in quality control.
Industrial Revolution and Transition to Factory System
The Industrial Revolution brought fundamental changes to quality control along with massive transformations in production. As the traditional artisan system gave way to factories, the need to control product quality increased. However, during this period, quality control was limited to inspecting products at the final stage, with defective products separated only at the end of the process. This approach did not ensure product quality, as production errors were often only detected during final inspection.
The 20th Century and the Birth of Statistical Quality Control
In the early 20th Century, quality control began to be approached with scientific methods. Walter A. Shewhart introduced the concept of Statistical Process Control (SPC) and recommended statistical methods in production processes. This marked the beginning of a shift in quality control from merely inspecting the product to focusing on analyzing and improving the process. W. Edwards Deming advanced Shewhart's work, and during World War II, statistical process control was successfully applied to military production processes. These practices made quality control an indispensable part of production processes.
Japan's Quality Revolution and the Rise of TQM (Total Quality Management)
After World War II, as Japan worked to rebuild its economy, it began using quality as a competitive advantage. Training from experts like Deming and Juran on statistical quality control and process improvement led to the adoption of a “Companywide Quality Control” approach in Japan. During this period, Japanese manufacturers embraced Total Quality Management (TQM) approaches, which aimed at product quality and continuous improvement across processes and the entire organization. This philosophy contributed to Japanese products gaining worldwide recognition for quality, inspiring other countries to enhance their quality control processes.
ISO 9000 and the Emergence of Modern Quality Standards
The 1980s and 90s saw the emergence of international standards for quality management. The ISO 9000 series became a global standard by defining the fundamental requirements organizations should adopt to manage quality. This standard ensured that products and services met customer expectations while promoting continuous improvement. Today, ISO 9001 is the most widely accepted standard for quality management systems and is a crucial reference in quality management.
Lean Manufacturing and the Rise of Six Sigma
Since the late 1990s, quality control and management have evolved into more sophisticated methodologies like Lean manufacturing and Six Sigma. Lean manufacturing aims to enhance efficiency by eliminating waste, while Six Sigma emphasizes minimizing process errors and fostering continuous improvement. These approaches focus on integrating quality control into production processes and the entire organizational structure, forming the foundation of quality management strategies for many organizations today.
Understanding Industry 4.0 and Quality 4.0
Industry 4.0
Industry 4.0 represents the fourth phase of the industrial revolution, characterized by integrating digital technologies into manufacturing environments. This era is defined by the convergence of advanced technologies, such as the Internet of Things (IoT), artificial intelligence (AI), robotics, and big data analytics, which facilitate the creation of smart factories. These technologies enable machines and systems to communicate with each other.
The term "Industry 4.0" originates from the concept of the Fourth Industrial Revolution, which significantly changes how products are manufactured and services are delivered compared to previous industrial phases. It encompasses not only machinery but also new manufacturing methods. Click here for more information about Industry 4.0.
Quality 4.0
Quality 4.0 is closely linked to advancements in Industry 4.0, focusing on integrating digital technologies into quality management systems. In this new phase of quality management, artificial intelligence, IoT, and big data are leveraged to automate and enhance quality processes in production. Quality 4.0 tools and systems enable real-time monitoring and predictive quality control, essential for maintaining high standards.
The implementation of Quality 4.0 facilitates smarter, more efficient quality management practices. These systems utilize sensors and connectivity to enable real-time data collection and analysis, allowing for rapid adjustments and improvements in production processes. Furthermore, Quality 4.0 integrates digital technologies that enhance the ability to monitor, measure, and analyze production variables, resulting in better outcomes.
These advancements redefine how products are made and how quality is managed in the modern industrial setting. Click here for more information on Quality 4.0 from an alternative source.
Key Components of Quality in Production
Document Management
A robust document management system forms the backbone of effective quality processes in production. Ensuring all critical documents are organized, up-to-date, and easily accessible supports the Plan-Do-Check-Act process at the heart of quality frameworks. Inadequate document control is associated with increased risks, regulatory compliance violations, and impacts on efficiency, emphasizing the need for a centralized document management system. Such a system safeguards documents and facilitates seamless collaboration across departments, ensuring compliance with industry standards like ISO 9001.
Training Management
Training is crucial for enhancing the quality of the products being produced. A comprehensive training management system boosts the workforce's skills, making them more agile and knowledgeable. Modern training management systems, often AI-supported and flexible, promote micro-learning and leverage technology to provide personalized, engaging, and practical training experiences. These systems ensure employees know the latest production practices and technologies, maintaining high production standards.
Corrective and Preventive Actions (CAPA)
Corrective and preventive actions are essential for addressing non-conformities in production processes and preventing potential issues. These actions involve systematically identifying, analyzing, and correcting quality problems to avoid recurrence and to ensure continuous improvement. Effective CAPA (Corrective and Preventive Action) systems are integrated with design controls and are supported by detailed investigations and verifications to ensure that the measures taken are appropriate and effective.
Change Management
Effective change management within quality assurance is crucial for adapting and implementing new processes and technologies that enhance product quality and compliance. This approach involves a structured method for transitioning teams and organizations to improved practices aligned with quality standards. Organizations can enhance productivity, boost employee morale, and improve overall quality outcomes by ensuring continuous improvement and engaging employees throughout the change process.
Quality 4.0 Integration in Smart Manufacturing
The Role of Enterprise Quality Management Systems
Enterprise Quality Management Systems (EQMS) are crucial for integrating Quality 4.0 into smart manufacturing environments. These systems leverage the capabilities of Industry 4.0 to enhance quality management through real-time monitoring and control of production processes. EQMS utilizes sensors at various stages of production to collect data on critical parameters such as temperature and pressure, and it can analyze this information using machine learning algorithms. This analysis helps identify patterns and potential anomalies that could lead to quality issues. Additionally, EQMS can trigger automatic corrective actions, such as adjusting production parameters or halting production, to mitigate these issues before they escalate, ensure compliance, and maintain high-quality standards.
Effects on Efficiency and Compliance
The integration of EQMS into smart factories significantly enhances efficiency and compliance. Real-time data collection and analysis facilitated by EQMS enable immediate quality control and process optimization. This system minimizes manual effort and reduces the likelihood of human error, leading to more reliable production outcomes. Additionally, EQMS supports compliance management by ensuring adherence to regulatory standards and maintaining audit readiness. The ability to provide traceability and transparency throughout the production process is essential for meeting quality and safety standards and environmental regulations.
Moreover, the proactive capabilities shaped by Quality 4.0 through EQMS go beyond mere technology application. They represent a shift towards more collaborative, competent, and strategically aligned quality management practices within organizational culture. This shift is vital for industries where high-quality and reliable products are crucial for customer satisfaction and brand loyalty. By integrating advanced analytics and artificial intelligence, EQMS enables organizations to adopt more adaptive, predictive, and proactive approaches in their quality management strategies, resulting in significant improvements.
Technological Developments Improving Quality
Automation and Data Analytics
Data analysis is crucial for improving quality control in the manufacturing sector. Manufacturers can monitor and enhance production processes, identify trends, and optimize resource allocation using statistical and computational tools. Tools such as Statistical Process Control (SPC) and Six Sigma methodologies effectively monitor and improve quality by tracking and analyzing process variables. They provide statistical significance, allowing for prompt corrective actions.
Additionally, a technique derived from data analysis called predictive maintenance plays a vital role in increasing production efficiency. Manufacturers can anticipate equipment failures before they occur, allowing for proactive maintenance and repairs, which minimizes downtime and reduces costs. Furthermore, data analysis aids in optimizing inventory levels and reducing waste, thereby enhancing overall production efficiency.
Cyber-Physical Systems (CPS)
Cyber-Physical Systems (CPS) enhance decision-making and quality control in manufacturing by integrating physical processes with networked digital technologies. These systems utilize sensors and controllers to collect data, which is then analyzed to optimize production tasks such as material handling, quality control, and assembly. The real-time monitoring and control enabled by CPS allows for dynamic adjustments in production processes while maintaining high quality.
The CPS architecture consists of multiple layers, from data collection to decision-making. In the cyber layer, data from all CPS devices is gathered, analyzed, and shared with devices for corrective actions, thereby increasing the reliability of production processes. This multi-layered approach enables CPS to respond to real-time changes and automate automation.
Conclusion
In conclusion, the exploration of integrating digital building blocks into manufacturing indicates that the incorporation of Industry 4.0 and Quality 4.0 into production processes represents a significant step toward achieving unprecedented levels of production quality and efficiency. By examining the roles of advanced technologies such as AI, IoT, EQMS, and CPS, our discussion emphasizes their critical contributions to improving how quality is managed, products are produced, ensuring compliance with ISO standards, and enhancing customer satisfaction. This strategic integration in smart manufacturing environments is not just a technological advancement; it signifies a transformative change in the industrial landscape and promises a future where digital and physical systems converge to establish new benchmarks for quality production.
Comentarios